Shoreline protection and recovery
Our solutions include two distinct technologies that work together to stop erosion and reverse it, re-growing coastlines the natural way.
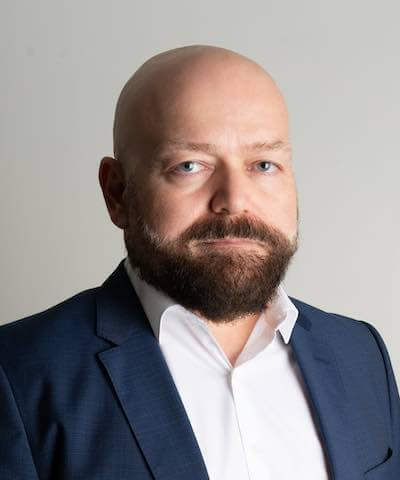
Primary inventor
Gene Avakyan - 26 years US Federal government, invention, and industry experience
US Federal Aviation Administration (in charge of all civil aviation in the United States)
US $13B in government contracts
Lead architect of all financial applications for City of Los Angeles’ City Attorney and Mayor’s office, all ports and airports
Received awards from City of Los Angeles’ City Attorney and Mayor’s office and from Mosaic Federation
UCLA Mechanical and Aerospace Engineering degree (‘Rocket scientist’)
Pepperdine University MBA (Master of Business Administration) degree
CEO of Edison Aerospace, aviation design and manufacturing company
WATCH OUR VIDEO NOW!IMPORTANT
HOW DOES IT WORK?TECHNOLOGY
TECHNICAL PRINCIPLES OF OUR SYSTEM
Each component in our system consists of a 2.5m long and 1.5m wide section made of biodegradable PHA plastic as shown below. Each section contains a vertical anchor fin that is submerged into the sandy bottom during installation.
The length of the anchor fins varies depending on the sea floor conditions, as different sea floor composition requires different levels of anchoring to secure the device to the sea bottom. After initial installation, as sand fills the internal cavity of the device, it will act as ballast as well, helping to keep the device firmly planted in the sea floor.
MATERIALS CHEMISTRY & SELECTIONTECHNOLOGY
There are two distinct materials we use to make the components of our system, depending on the goal of the client.
• Polyhydroxyalkanoates (PHA) plastic is made from biosynthesized and carbon-rich renewable resources. It breaks down into carbon dioxide and water.
• Polylactic acid (PLA) plastic is made from renewable biomass containing plant starches. It breaks down into carbon dioxide, lactic acid (sugars), and water, but slower.
If the goal is to keep growing the beach by installing our system after sand has fully covered the first layer of our components, we use biodegradable PHA plastic that will fully dissolve underwater in approximately 1 year. After sand has covered the initial components, the next layer can be installed, which will continue growing the beach by building up a further layer of sand.
Once the client has decided on not growing the beach any longer and we want to grow and hold the beach at a given size, we use non [fully biodegradable] PLA plastic that will retain its form for longer, maintaining the newly formed beach level for several years.
INSTALLATIONSystem
A particular advantage of our system over other methods such as slurry-filled geotubes and dredging is that we require no heavy machinery to be used on the beach, further damaging it in the process.
Our system consists of relatively lightweight components that are installed by hand by a pair of workers moving each piece into place along a designated and marked line that runs from the shore out along the bottom from 20m to 50m, depending on specific location topography (Figs 4 and 5).
Simulation of workers manually installing SPT System. Fig 4
Installed SPT System in near-shore environment
PHYSICAL PRINCIPLESTech
Our system works by interrupting the longshore current (running along the beach) that is created by the energy of the waves hitting the shoreline at oblique angles (Fig 1).
The reason for sand transport and erosion that is created by the longshore current is that the natural sand flow along the coastline is disrupted by man-made structures and other alterations to the coastline (Figs 2 and 3).
Our goal is to use natural principles to compensate for effects of man-made interruptions to the flow (fig 2, 3).
Waves approaching beach have a normal component (at right angle to beach), and longshore component (along the beach) Fig 1
Effects of port construction on Jumeirah beach Fig 2
Interrupting sand transport mechanism with structures affects sand distribution and erosion Fig 3
Historically, shorelines have achieved a natural balance between land and water that was only interrupted when storms would alter the underwater topography, thus changing the sand transport mechanism and with it the shape of the coast. With large-scale man-made alterations, this balance was altered forever in favor of human engineering, forcing it to be implemented more and more to keep nature in check.
Technical PrinciplesTech
Our solution to controlling and reversing sand erosion is to interrupt the longshore current as gently as possible, causing only the transport of sand to be affected, without affecting the ecosystems found on-shore, in the swash zone, and in the near-shore zone.
Our patented device can be regarded as acting like a ‘speed bump’ that slows down the fluid traveling over it by creating vortices to form over its cylindrical surface (Fig 4 and 5).
Computational flow model testing. Fig 4
Actual flow testing. Fig 5
These vortices force the locally slowed flow of water to drop the grains of sand that it is carrying. These dropped grains of sand are deposited near the device, causing the sea bottom to rise until reaching above the device’s height above the sea floor. This, in turn, has the effect of raising the sea floor slowly and naturally without harming any of the creatures that call that eco-system home.
Our in-house testing of prototypes of the device has demonstrated high effectiveness even when tested in non-scale conditions that simulated more difficult conditions than encountered in real life.
Computational flow model testing. Fig 4
COMPONENT DESIGNDESIGN
Dimensions of one component of the SPT System; approximate weight: 35kg. Fig 7
OTHER METHODS OF CONTROLLING EROSIONProblem
Past engineering solutions to erosion control relied on using an overabundance of force in place of finesse. These methods include dredging, building groynes, sea walls, and gabions. The prevalent method of beach nourishment around the world today is dredging.
Dredging
The problem with dredging is that first, it damages the underwater ecosystem, killing off vital sea life, second, by dumping tons of sand onto the beach, it buries many small organisms alive, killing them in the process. Finally, by lifting layers of sand from the sea floor, the process also disturbs the heavy metal deposits that settled there, creating a toxic environment underwater and exposing beachgoers to the same toxins.
These three negative externalities, along with the high cost of dredging and the need to repeat the process every six months to a year, are the primary reason why dredging should be the last option selected by a government or municipality when considering how to stop and reverse beach erosion.
Dredging in use to put new sand onto a beach
Groynes
The problem with above-water groynes is their unsightly appearance and interference with public usage of the beach. The image below demonstrates why groynes are not a good option – they interfere with bathers, surfers, windsurfers, and even people strolling down the beach.
Constructing groynes, which are typically made from stone or wood, is also far more expensive than the proposal outlined herein. Wooden groynes require constant upkeep and replacement of planks as they wear out due to their submersion in the seawater.
Wooden groynes
Sea walls and gabions
Sea walls are the most expensive and permanent method of controlling erosion and rising sea levels. This method makes no attempt at recovering or restoring the shoreline, and is more of a last line of defense in the war man wages against nature.
The astronomically high costs to build sea walls is justified only in the most extreme cases where erosion has encroached too close to human habitation or industry and where there is no opportuninty to use sand transport to build out a sandy beach, thus creating a buffer space between the ocean and human development. This is the case where there is no sand available for the transport mechanism to carry, for example.
Sea walls and gabions
Materials in Use / SuppliersSuppliers
The components for installation in the United Arab Emirates and the United States will be manufactured from a marine biodegradable product called PHA ( Polyhydroxyalkanoates
, or more specifically P3HB), that breaks down in a marine environment into water and carbon dioxide.
To this end we have initiated discussions with several producers of PHA pellets such as Mango Materials and Danimer Scientific. For prototyping purposes, PLA and PLA+ was used to produce components on 3D Printers.
PLA producers are easier to source, and we are considering acquiring raw materials from NatureWorks or Futerro.